MODERN PTFE MEMBRANE BASED HEPA/ULPA FILTERS FOR IMPROVED ENERGY SAVINGS AND RISK REDUCTION
Authors:
Marc Schmidt, Ph.D., Sean O'Reilly, Mike Osborne, Ph.D., Jonathan Rajala, Ph.D.Keywords:
ePTFE and eFRM HEPA filters, risk reduction, energy savings, mechanical and chemical resistanceAbstract:
Strict demands are put on HEPA/ULPA filters that are installed as terminal filters in cleanrooms, isolators, workbenches etc. or as last filter stage in air handling units being upstream. They must continuously guarantee safe operation while predefined air quality requirements and energy efficiency are optimized. For that the filter media itself is of major importance.Standard filter media for HEPA/ULPA filters so far had been fiberglass paper. Being free of boron filter media based on expanded Polytetrafluoroethylene (ePTFE) is used in microelectronics since decades. Based on latest developments in membrane technology, such as PAO compatibility, ePTFE and expanded Fluoro-Resin Membrane (eFRM) based HEPA filters are on their way to replace fiberglass-based filters.
This presentation describes how ePTFE and eFRM membrane media contributes to process safety and low-cost operation.
It sets out structure of modern ePTFE and eFRM membrane media, how these air filters provide significant reduction in energy consumption and risk.
It presents results of several studies on superior stability, durability and performance of ePTFE and eFRM media over traditional fiberglass media. Based on several tests regarding mechanical and chemical resistance as well as soot loading it is demonstrated that ePTFE and eFRM media offer a significant improvement in reducing media failure risk for a retained filter integrity.
Article:
PTFE, EXPANDED PTFE (ePTFE) AND EXPANDED FLUORO-RESIN (eFRM) MEDIA
On April 6, 1938 Dr. Roy Plunkett, a scientist with chemicals company DuPont®, accidently discovered polytetrafluoroethylene (PTFE) while looking for better cooling agent. Leaving a batch of tetrafluoroethylene (TFE) gas in a pressure container overnight, he found the next day a layer of a white translucent waxy solid: Polymerized TFE, i.e. PTFE. Polytetrafluoroethylene was abbreviated to Teflon® as registered as trademark in 1945. Today PTFE is available by numerous suppliers under different trademarks.
Its chemical structure is a fluorine saturated carbon chain (C2F4)n of high molecular weight. Fluorine atoms, strongly bond to the carbon atoms, surround the central ethylene carbon chain completely protecting it from chemical attacks.
Traditional glass fiber based HEPA-/ULPA-filter media are made of SiO2 fibers. With progress in microelectronics outgassing issues of boron (Br), an accompanying element of silicon (Si), created quality problems in production of microelectronic components.
In Oct 1969 Mr. Bob Gore accidently discovered expanded PTFE (ePTFE). Frustrated with rods breaking when being stretched too slowly, he quickly draws a hot PTFE rod and found he can stretch PTFE 1000-times its original length. First commercial product in 1970 was PTFE pipe tape sealant. Today it's a commodity used in nearly every household. In 1973 industrial filter bag business begun. Here expanded PTFE is used for filtration, pioneering membrane surface filtration to capture contaminants and other particles. Since 1976 ePTFE in apparel is used.
In 1994 ePTFE membrane HEPA-/ULPA-filter for deep filtration, made by Japanese Daikin Industries, revolutionized filtration for microelectronic cleanrooms due to ultralow low emission of volatiles, particularly Br.
Nowadays membrane HEPA filters based on expanded Fluoro-Resin Membrane (eFRM) became available from Daikin Industries. These are overcoming some issues with ePTFE filters regarding clogging when leak tested with photometers, which use high concentrations of oily PAO test aerosols, as well as regarding use in pure fresh air applications.
ePTFE AND eFRM MEMBRANE FILTER MEDIA
Figure 1 shows a SEM photo of whole ePTFE HEPA filter membrane media. For comparison a human hair is shown.
The very fine three-dimensional network of PTFE fibrils is bound by small PTFE nodes. Just for stiffening and pleatability ePTFE membrane is supported by a nonwovens layer. That layer doesn't contribute significally to filtration efficiency.
The whole media has a depth of about 100µm. That's 1000-times the diameter of a 0,1µm particle. Thus, ePTFE HEPA filter membrane media is providing deep filtration - no surface filtration!
Figure 1: ePTFE HEPA filter membrane media
eFRM media is composed of similar structure but there are two layers of fine-tuned expanded fluoro-resin membrane (eFRM) for improved depth filtration.
Figure 2 shows a SEM photo of ePTFE membrane (left) and traditional glass fiber media (right).
Clear difference in structure can be seen. ePTFE membrane has much smaller pore size than glass media, in average 0,5 - 1µm; i.e. about 100 million pores per cm2. About 1.000-2.000 of such pores would fit across the tip of a ball point pen.
But more important for filtration is the fiber diameter. Diameter of traditional glass fibers is in the range of 0,5 -1µm; whereas ePTFE fibrils diameter is in the range of 20 - 200nm.
These ultra-thin ePTFE fibrils provide excellent filtration efficiency, particularly for very fine particles but also create an extremely low pressure drop by slip-flow effect.
Figure 2: ePTFE membrane (left) and traditional glass fiber media (right)
SLIP FLOW VS VISCOUS FLOW
At typical air flow velocities for HEPA filtration viscous flow regime is formed around traditional glass fibers (Figure 3). The air flowing around the fibers can be seen as a continuum following laws of classical fluid dynamics.
Figure 3: Boundary layer at viscous flow around traditional glass fiber
With viscous flow regime air velocity at the very surface is equal to zero. With increasing distance from the surface, the velocity increases up to velocity of free flow field; forming so called boundary layer. Velocity gradient within the boundary layer leads to internal friction resulting in energy dissipation, which is causing significant pressure drop.
With ultra-thin ePTFE or eFRM fibrils air cannot be seen as continuum anymore. Furthermore, discrete air molecules and their behavior based on kinetic gas theory have to be considered. According kinetic gas theory, gas molecules do randomly move around their flow lines. They collide within a characteristic distance, called mean free path, with each other. That behavior is also called Brownian motion of gas molecules.
Under ambient conditions mean free path of air molecules is about 68nm. With diameter of ePTFE or eFRM fibrils of 20-200nm these are in the same range of size than mean free path of air. Under these circumstances a different flow regime, called slip flow is formed.
With slip flow regime air velocity at the very surface is not equal to zero. Thus a boundary layer is not fully formed resulting in less internal friction and less energy dissipation (Figure 4). Result is dramatic decrease of pressure drop up to 50%.
Figure 4: Slip flow regime around ultra-thin PTFE fibril
Slip flow regime and its effect on air filtration is already known since decades (Brown, 1993; Kirsch et al.,1973) and was just recently experimentally confirmed (Bao et al., 2016).
Significant effect of slip flow regime can be seen at Knudsen numbers above around 1:
(1)
With above mentioned diameters for ePTFE fibrils and mean free path of air under ambient conditions, range of Knundsen number is:
(2)
Mean free path of air at ambient conditions is given the under real world conditions. Thus, slip flow regime can only be formed when fiber resp. fibrils are ultra-thin. As glass fibers cannot be spun with necessary ultra-fine diameters, formation of fibrils by expanding PTFE or FRM membrane is an excellent way for manufacturing highly filtration effective and energy efficient HEPA filter media.
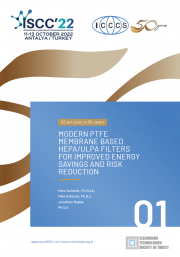